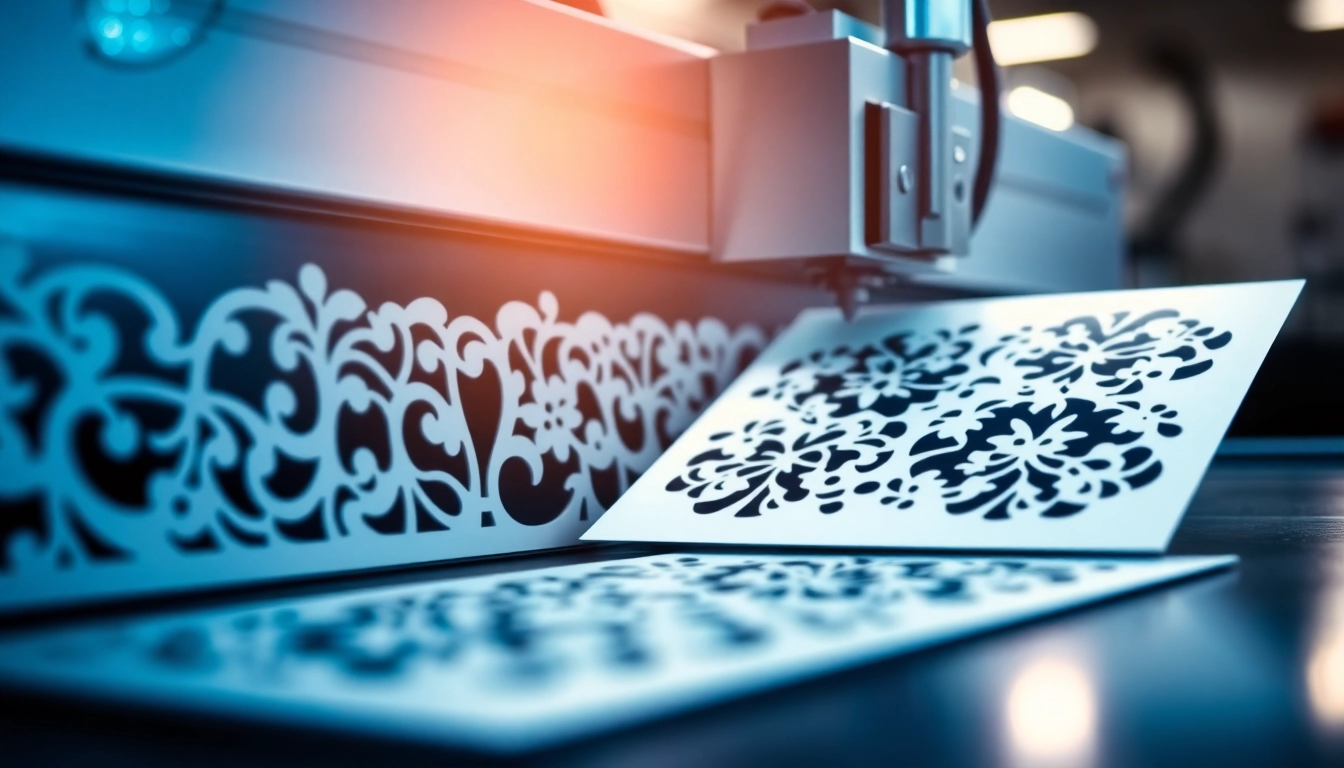
Understanding Precision Die Cutting
Precision die cutting is an engineered process that transforms flat sheets or rolls of material into specific shapes using sharp blades. This method is pivotal in various manufacturing sectors, facilitating the production of intricate designs with remarkable accuracy and efficiency. Whether you require customized gaskets, components for electronic assemblies, or packaging materials, precision die cutting has become a go-to technique due to its versatility and precision.
What is Precision Die Cutting?
At its core, precision die cutting involves the use of dies—metal templates that cut through material with incredible precision. This process can handle a wide variety of substances, including paper, plastic, rubber, and even thin metals. The method is commonly employed in commercial printing, packaging, and product manufacturing industries. By utilizing different cutting techniques like rotary, flatbed, and laser die cutting, manufacturers can cater to unique specifications that high-volume productions often require.
Applications in Various Industries
Precision die cutting finds applications across numerous industries:
- Automotive: Gaskets, seals, and insulation materials.
- Electronics: Custom cut components for circuit boards, insulating materials, and housing.
- Healthcare: Die-cut components for medical devices and packaging of pharmaceutical products.
- Packaging: Creating custom boxes, labels, and other packaging materials tailored to fit specific products.
- Textiles: Custom shapes for fabrics and upholstery pieces.
Benefits of Precision Die Cutting Over Other Methods
Choosing precision die cutting offers several advantages such as:
- High Accuracy: Minimal tolerances effectively reduce material waste and ensure parts fit perfectly.
- Speed: High-volume productions can be completed much faster compared to manual cutting methods.
- Consistency: Uniformity in production leads to high quality and reliability in the final output.
- Cost-Effectiveness: Despite initial setup costs, long runs reduce per-piece costs dramatically.
- Customization: Ability to produce complex shapes that meet specific client needs without significant alterations in tooling.
Types of Precision Die Cutting Techniques
Rotary Die Cutting Explained
Rotary die cutting is a process that employs cylindrical dies to cut through material continuously as it passes through the machine. This technique is particularly beneficial for long runs and is often combined with other decorating processes, such as printing. One of the major advantages is the speed and efficiency it offers, producing high volumes with less waste. Industries that commonly utilize rotary die cutting include packaging and label production.
Flatbed Die Cutting Analysis
Flatbed die cutting involves using a reciprocating die that presses down onto the material, cutting patterns as it goes. This method allows for greater design flexibility, making it ideal for intricate shapes and smaller batches. Though generally slower than rotary die cutting, it is versatile, enabling manufacturers to handle various thicknesses and larger sheets. Flatbed die cutting is commonly used for creating prototypes and producing short runs of specialized parts.
Laser Die Cutting Innovations
Laser cutting technology has revolutionized the die cutting industry by introducing enhanced precision. Using high-powered lasers, this technique excises designs from materials without the need for physical dies, making it suitable for prototyping and small production runs. Laser die cutting provides quality cuts with minimal kerf, ensuring even the most detailed designs are accurately rendered. It’s widely used in the aerospace, automotive, and artistic sectors for creating precisely detailed components.
Key Materials Used in Precision Die Cutting
Common Materials for Die Cutting
Precision die cutting accommodates a variety of materials. Commonly processed materials include:
- Papers and Cardboards: Extensively used in packaging, labels, and promotional materials.
- Plastics: Acrylics and polyethylenes are frequently cut for packaging and casing.
- Foams: Utilized in automotive and cushioning applications.
- Metals: Thin sheets of aluminum or steel for intricate components in heavy-duty applications.
Choosing the Right Material for Your Project
Selecting the appropriate material is crucial for achieving desired performance. Factors to consider include:
- Application Requirements: Will the part endure stress, temperature variations, or exposure to chemicals?
- Physical Properties: Consider weight, thickness, and flexibility of the material for optimal results.
- Finish: Evaluate the aesthetic and tactile preferences needed for the final product.
Material Performance and Precision
The choice of material directly influences the precision of outcomes in die cutting. Factors like material thickness and density affect how effectively dies can cut through them. Materials with higher tensile strength may require more robust dies and potentially additional processing time, bringing considerations for balancing performance with production efficiency.
Precision Die Cutting Tolerances and Quality Control
Understanding Tolerances in Die Cutting
Tolerances in precision die cutting refer to the permissible limit within which the die-cut parts can vary from desired dimensions. Typically, tolerances for precision die cuts range from ±0.005 inches, with variations influenced by the material used and the specific die cutting method applied. Understanding these tolerances is critical for ensuring that the parts meet functional specifications.
Quality Control Processes in Precision Die Cutting
To maintain quality standards, implementing rigorous quality control processes is essential. This can include:
- Regular Equipment Inspections: Ensuring machinery remains calibrated for optimal performance.
- Visual Inspections: Identifying defects or inconsistencies in parts.
- Measurement Checks: Utilizing precision tools to verify that dimensions conform to the specified tolerances.
Improving Accuracy with Technology
Modern technologies, including computer-aided design (CAD) and machine learning, can vastly enhance accuracy in die cutting processes. CAD allows for precise designs that can be fed directly into die cutting machines, minimizing human error. Additionally, implementing automated quality checks using imaging technologies can significantly increase the reliability of the production process.
Cost Considerations for Precision Die Cutting Services
Factors Influencing Die Cutting Costs
The cost of precision die cutting services can fluctuate based on various factors, including:
- Material Type: More specialized or durable materials can increase costs.
- Die Complexity: More complex die designs require higher initial investments, which can affect overall pricing.
- Volume of Production: Higher quantities often lead to reduced per-piece costs.
Long-term Value of Precision Die Cutting
While initial costs can be a concern, precision die cutting typically provides long-term value through improved efficiency and reduced material waste. Higher quality components also enhance the longevity and reliability of final products, resulting in improved customer satisfaction and reduced returns.
Finding a Cost-effective Die Cutting Partner
When seeking a partner for precision die cutting, it’s vital to evaluate their capabilities, experience, and technology utilization. Consideration should also be given to their flexibility in accommodating different project sizes and their adherence to quality standards. Establishing a partnership with a reliable die cutting service can lead to sustained cost savings and enhanced product quality over time.