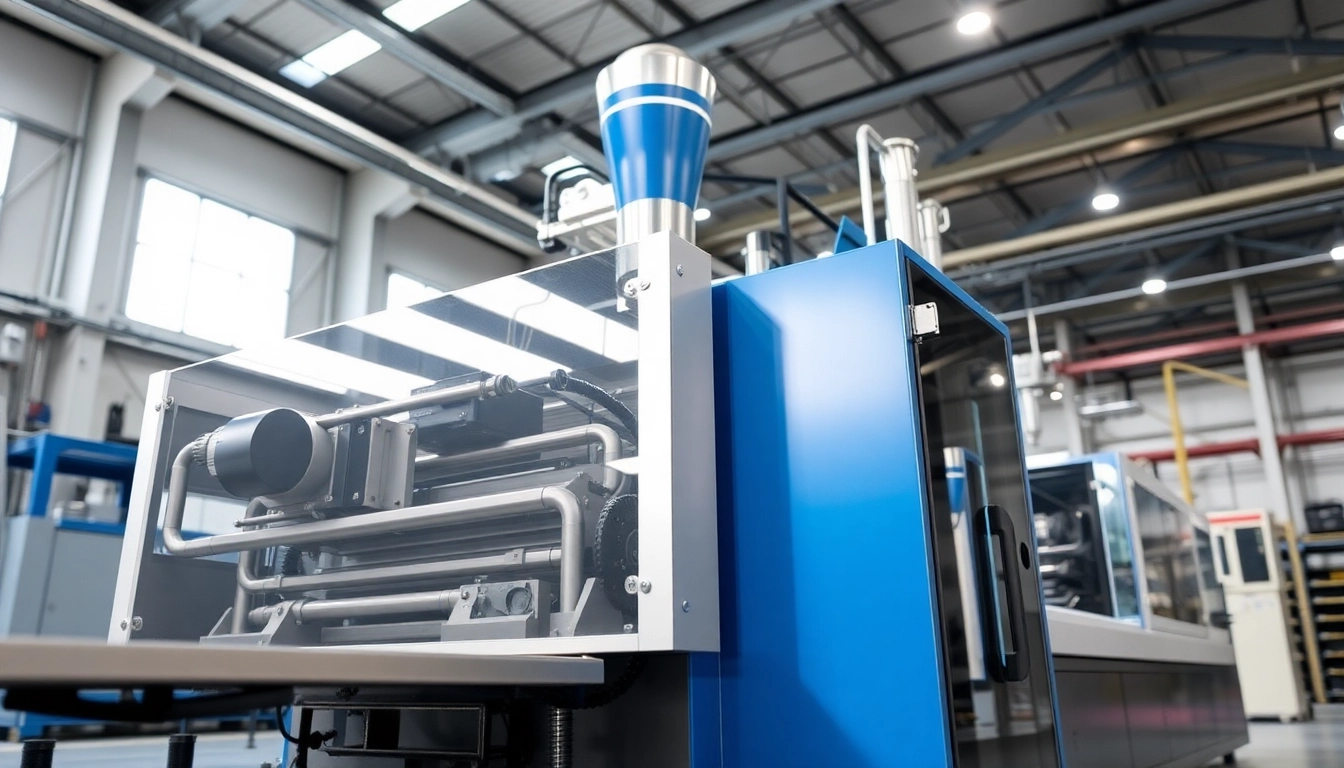
Understanding Blow Molding Technology
What is Blow Molding?
Blow molding is a manufacturing process used to create hollow plastic products, predominantly in the production of containers, bottles, and various industrial parts. The process involves forming a piece of plastic into a parison— a tube-like structure—and then inflating it within a mold through the application of air pressure. This innovation allows manufacturers to produce lightweight yet strong products efficiently. As industries increasingly prioritize efficiency and functionality, understanding the intricacies of blow molding becomes paramount. For those seeking superior machinery, turning to a reliable Blow Molding Machine Manufacturer ensures access to cutting-edge technology and support.
Types of Blow Molding Processes
There are three primary types of blow molding processes, each suited for different applications:
- Extrusion Blow Molding (EBM): This common method involves extruding plastic into a parison which is inflated to form the desired shape. EBM is widely used for producing bottles and containers of various shapes and sizes.
- Injection Blow Molding (IBM): This process combines injection and blow molding techniques. A preform is created using injection molding, which is then blown to achieve the final form. IBM is ideal for precision applications, such as pharmaceutical and cosmetic packaging.
- Stretch Blow Molding (SBM): This process involves stretching the preform axially and then blowing it into the mold. It’s particularly beneficial for producing high-strength containers, commonly employed in beverage industries.
Application Areas of Blow Molding
Blow molding finds applications across a variety of sectors:
- Packing and Beverage Industry: From water bottles to detergent containers, blow molding is a go-to method for creating packaging that meets both aesthetic and functional needs.
- Toys and Consumer Goods: Lightweight and colorful items produced through blow molding appeal to the consumer market, allowing for diverse designs at low production costs.
- Automotive Industry: Components like fuel tanks and air ducts often utilize blow molding for their durability and light weight.
- Medical Field: Blow molding technology is instrumental in producing sterile containers and equipment, ensuring safety and precision.
Choosing the Right Blow Molding Machine
Factors to Consider When Selecting a Machine
The selection of a blow molding machine is critical for maximizing productivity and quality. Here are key factors to consider:
- Production Volume: Determine your production needs—high-volume output may necessitate a more advanced, automated machine.
- Material Compatibility: The chosen blow molding machine should accommodate the types of materials (e.g., PET, HDPE) you plan to use.
- Machine Size and Configuration: Consider the physical space available in your operation and the specific configurations (e.g., single-station vs. dual-station) that will suit your production line.
- Energy Efficiency: Opt for machines that are designed for energy efficiency, reducing long-term operational costs.
Key Features of High-Quality Blow Molding Machines
Technological advancements have resulted in blow molding machines that offer numerous features to enhance efficiency and product quality:
- Servo-driven Technology: This feature allows for precise control of the machine’s functions with reduced energy consumption.
- Multi-layer Capability: Machines that support multi-layer bottle production enhance packaging performance by permitting additional barrier properties.
- User-friendly Interfaces: Advanced control panels enable operators to manage processes more efficiently, with easy access to diagnostics and troubleshooting.
- Automated Material Handling: Implementing automatic loading systems can significantly reduce labor costs and minimize human error.
Common Mistakes in Machine Selection
Even seasoned manufacturers can make missteps when selecting blow molding equipment. Common challenges include:
- Underestimating Future Production Needs: Machines should not only meet current production requirements but also account for projected growth.
- Ignoring Maintenance Protocols: Selecting a machine that does not allow easy maintenance can lead to prolonged downtimes and repairs.
- Overlooking Operator Training: Subsequent challenges in operation can arise if operators are not adequately trained in machine functionalities.
Top Blow Molding Machine Manufacturers in the Industry
Industry Leaders: Who to Know
The global market for blow molding machines is populated by several renowned manufacturers. Among them, notable companies include:
- Uniloy: Esteemed for offering diverse blow molding technologies, Uniloy leads in selling blow molds and the associated tooling.
- Wilmington Machinery: Specializing in high-speed monolayer and multilayer rotary extrusion machines, Wilmington is a renowned name in high-performance engineering.
- Jomar Corporation: Celebrating over 50 years in manufacturing injection blow molding machines, Jomar is known for solid and reliable products.
- Graham Engineering: Known for innovative solutions like the Graham Wheel rotary blow molder, Graham Engineering excels in producing perfectly formed parisons.
Comparing Product Offerings
When it comes to product comparisons, here are aspects to explore:
- Flexibility: Some manufacturers offer machines that can easily switch between processes (e.g., EBM and IBM).
- Customization: Look for manufacturers that provide tailored solutions to meet specific business needs.
- After-sales Support: Assess the availability of maintenance support, warranty options, and customer service responsiveness.
What Differentiates Each Manufacturer?
While many manufacturers produce similar machinery, distinguishing features often include:
- Technological Innovations: Some brands prioritize ongoing R&D to stay ahead with technological advancements.
- Your Industry Focus: Certain manufacturers may specialize in distinct sectors, such as medical or food and beverage, influencing their product designs.
- Sustainability Practices: Companies committed to eco-friendly practices stand out, as consumers increasingly demand sustainability in production processes.
Cost Considerations and Investment Value
Understanding Blow Molding Machine Pricing
Investing in blow molding machines requires sound financial consideration. Pricing can vary widely and depend on several factors:
- Machine Type: Basic machines for small-scale production might start at tens of thousands, while advanced automated systems can reach into the hundreds of thousands.
- Customization: Custom-built machinery tailored to specific production needs will typically incur higher expenses.
- Brand Reputation: Well-established manufacturers often charge a premium for their products due to quality assurances.
Calculating Return on Investment (ROI)
When evaluating the ROI on a blow molding machine purchase, consider both quantitative and qualitative factors:
- Production Capacity Increases: Higher output often balances the machine’s cost and can significantly improve revenue.
- Operational Savings: Assess savings from energy efficiency and reduced labor costs over operating periods.
- Quality Improvements: Higher quality products may lead to fewer customer complaints and returns, enhancing brand loyalty.
Financing Options for Equipment Purchase
Understanding the financing options available can ease the capital burden associated with acquiring blow molding machines:
- Leasing: Leasing machinery can provide the necessary flexibility for businesses that hesitate to make a full upfront investment.
- Loans: Traditional bank loans or equipment financing solutions can help spread the cost over time.
- Grant Programs: Some regions offer financial assistance or grant programs aimed at businesses investing in sustainable or technologically advanced manufacturing.
Future Trends in Blow Molding Manufacturing
Technological Innovations and Their Impact
The landscape of blow molding technology is rapidly evolving, driven by technological advancements such as:
- Industry 4.0: The integration of IoT in manufacturing provides real-time data analytics, fostering smarter operations. This shift allows manufacturers to adopt predictive maintenance strategies and optimize production lines.
- 3D Printing for Molds: 3D printing technology is revolutionizing the traditional mold-making process, allowing for faster prototyping and reduced costs.
- Advanced Materials: Emerging polymer materials with specialized properties allow for innovation in product design and functionality.
Environmental Considerations in Blow Molding
With a growing emphasis on sustainability, the blow molding industry is adopting environment-friendly practices:
- Recyclable Materials: Many manufacturers are now designing blow molding machines that can process recyclable materials, fostering a closed-loop system.
- Reduced Emissions: Innovations aimed at reducing carbon footprints during production processes are increasingly prioritized by leading manufacturers.
- Efficient Water Usage: Emerging technologies focus on minimizing water use in cooling processes, addressing another significant environmental impact.
Adapting to Market Changes in Packaging
The blow molding industry must remain flexible to adapt to ongoing shifts within the packaging market, which include:
- Consumer Preferences: An increasing demand for eco-friendly packaging necessitates innovation within blow molding processes, focusing on biodegradable and recycled materials.
- Market Dynamics: Shift towards smaller, more convenient packaging solutions is pushing manufacturers to develop machinery capable of producing diverse sizes and designs.
- Global Standards: As regulations evolve globally, manufacturers need to comply with new standards that promote sustainable packaging and efficient production.