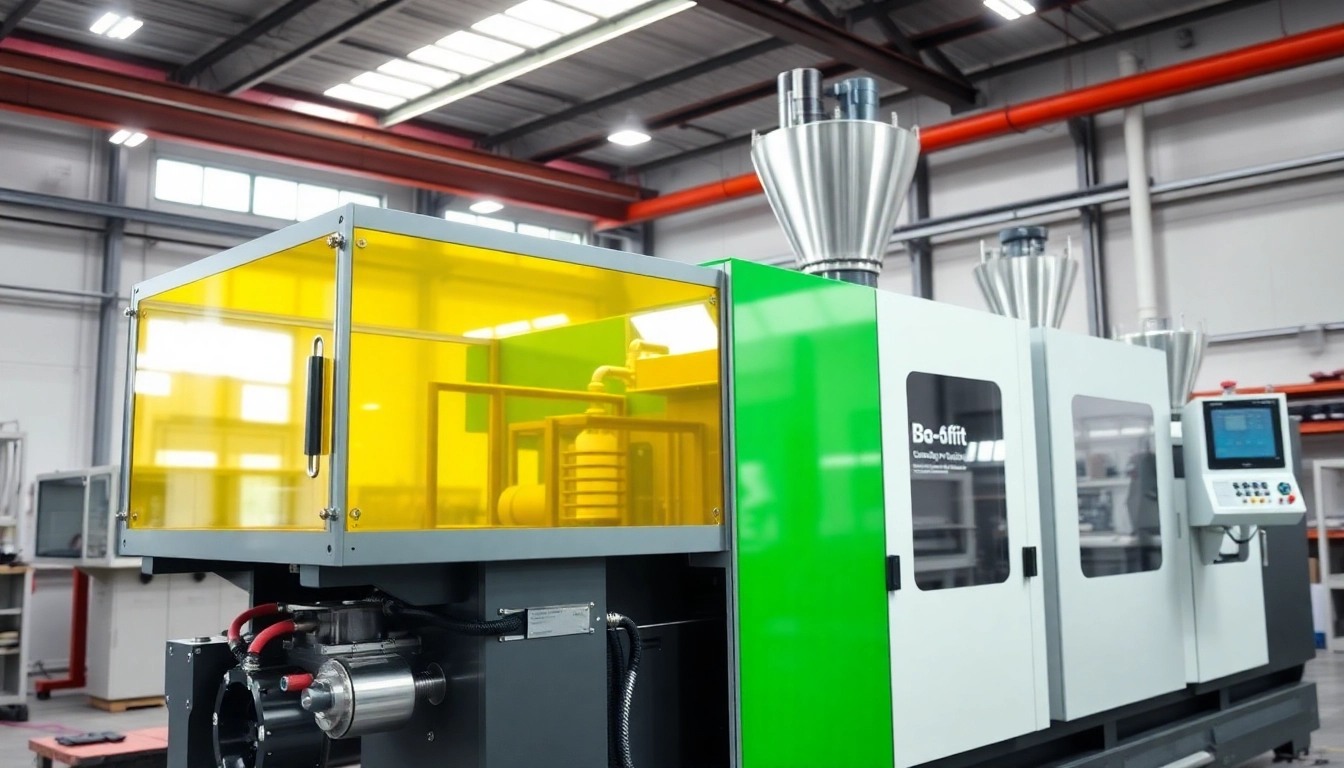
Understanding Blow Molding Technology
What is Blow Molding?
Blow molding is a manufacturing process used to create hollow plastic parts by expanding molten thermoplastic material into desired shapes. It is primarily used for producing containers like bottles, tanks, and hollow objects at a large scale. The process involves melting plastic pellets into a pliable form, allowing manufacturers to shape them into numerous designs efficiently. As you explore the fascinating world of manufacturing, discover more about the role of a Blow Molding Machine Manufacturer in this domain.
Types of Blow Molding Processes
There are three primary methods of blow molding: extrusion blow molding (EBM), injection blow molding (IBM), and stretch blow molding (SBM). Each technique employs a distinct method in shaping the plastic, catering to different needs within the manufacturing industry.
- Extrusion Blow Molding (EBM): This process begins with melting plastic pellets and forming a parison, which is then clamped into a mold. Air is injected to expand the plastic, resulting in a hollow object. EBM is favored for producing large containers and complex shapes.
- Injection Blow Molding (IBM): This method combines injection molding and blow molding. A preform is shaped using injection molding, and then air is blown into the preform to create the final shape. IBM is typically used for smaller bottles where precision is crucial.
- Stretch Blow Molding (SBM): SBM is a specialized form of manufacturing often used for PET bottles. It stretches the preform during the blowing stage, enhancing the molecular orientation, which increases strength and transparency.
Applications of Blow Molding in Industry
Blow molding finds diverse applications across various sectors, significantly impacting how we package and handle products. Industries making use of blow molding include:
- Food and Beverage: PET bottles for soft drinks, water, and other beverages are commonly produced through blow molding.
- Cosmetics: Many cosmetic products require customized packaging, making blow-molded containers a popular choice for creams, lotions, and sprays.
- Pharmaceutical: Blow molding is also leveraged for producing bottles for medicinal products, ensuring safety and compliance with regulations.
- Industrial Products: Various industrial products such as fuel tanks, chemical containers, and more are fabricated using blow molding.
Choosing the Right Manufacturer
Key Features to Look for in a Blow Molding Machine
Choosing the right blow molding machine depends on several key features tailored to your production needs:
- Machine Type: The choice between EBM, IBM, or SBM can significantly affect production efficiency depending on the desired product.
- Output Capacity: High-output machines can streamline production, reducing operational costs.
- Precision and Quality: Look for machines that ensure precise dimensional accuracy and high-quality finishes to enhance product appearance.
- Energy Efficiency: Modern blow molding machines incorporate energy-efficient technologies, leading to reduced operational costs over time.
- Ease of Use and Automation: User-friendly controls and automation features can enhance efficiency and reduce downtime.
Evaluating Manufacturer Reputation
When considering a blow molding machine manufacturer, reputation is critical. Researching manufacturer history, reading customer reviews, and evaluating their experience within the industry can provide insights into their reliability:
- Industry Experience: Established manufacturers with years of experience tend to offer more reliable equipment and support.
- Customer Testimonials: Real-world experiences from current users can inform potential buyers about machine performance and service levels.
- Partnerships and Certifications: Manufacturers that partner with leading industry players or have relevant certifications are often more trustworthy.
Cost vs. Quality Considerations
When it comes to investment in blow molding machinery, balancing cost and quality is paramount. Understand that choosing cheaper options might lead to lower quality, resulting in higher long-term costs due to repairs and lower efficiency:
- Initial Investment: Consider the upfront machine cost, installation, and potential customization fees.
- Long-Term Costs: Analyze operational, service, and maintenance costs to understand total expenses related to the machine.
- Return on Investment (ROI): Calculate the expected ROI based on productivity gains, reduced waste, and overall performance enhancements.
Advantages of Working with a Reliable Manufacturer
Benefits of High-Quality Machines
Investing in high-quality blow molding machines from reputable manufacturers ensures greater reliability, efficiency, and production quality. Some benefits include:
- Improved Production Speed: Reliable machines can significantly increase throughput, meeting production targets more effectively.
- Consistency: A high-quality machine provides consistent product outputs, enhancing brand reputation through product reliability.
- Durability: High-quality engineering often results in machines that withstand the rigors of continuous operation over many years.
After-Sales Support and Service
After-sales support is crucial in minimizing downtime and ensuring smooth operations. A good manufacturer will provide:
- Comprehensive Training: Ensuring employees are well-trained minimizes the risk of operational issues.
- Timely Maintenance: Scheduled maintenance checks and quick response times for service requests are vital for minimizing downtime.
- Access to Spare Parts: Reliable manufacturers should offer parts supply for machine upkeep.
Customization Options for Unique Needs
Every production line has unique requirements. A reliable blow molding machine manufacturer should offer customization options to meet specialized needs:
- Machine Modifications: Adjustments to accommodate different product sizes, shapes, and materials.
- Software Updates: Offering the latest technological advancements for optimized machine performance.
- Training Programs: Custom training programs tailored to specific production challenges can enhance operational efficiency.
Case Studies: Success Stories in Blow Molding
Innovative Solutions from Leading Manufacturers
To illustrate how technology can drive production efficiency, consider various success stories from notable blow molding manufacturers:
- Brand A: Implemented automation, reducing labor costs by 30% while increasing production speed.
- Brand B: Integrated energy-efficient systems that reduced energy consumption by over 20%, leading to significant operating cost savings.
- Brand C: Customized machines to produce a new line of eco-friendly containers, successfully capturing a niche market.
Real-World Applications and Results
Examining real-world applications sheds light on how blow molding is revolutionizing product development:
- Pharmaceutical Containers: Enhanced sealing and safety features increased compliance with FDA regulations for medication packaging.
- Custom Bottles: Novel designs tailored to specific product requirements resulted in higher market penetration and increased sales.
- Industrial Tanks: Improved structural integrity allowed for larger capacity tanks without compromising safety standards.
Lessons Learned and Best Practices
Through these success stories, several best practices emerged:
- Invest in Training: Continuous employee training is critical in utilizing new technologies effectively.
- Focus on Sustainability: Manufacturers are increasingly looking to create eco-friendly products to meet market demands.
- Regular Feedback Loops: Establishing channels for operational feedback can lead to continuous improvement in processes.
Future Innovations in Blow Molding
Industry Trends to Watch
As the manufacturing landscape evolves, several trends are shaping the future of blow molding, including:
- Smart Manufacturing: The incorporation of Industry 4.0 principles will lead to greater efficiencies and data-driven decision making.
- Increased Demand for Sustainability: Eco-friendly materials and processes are expected to gain prominence as consumers prioritize sustainability.
- Customization and Flexibility: With customer preferences becoming more individualized, manufacturers will be driven to produce unique designs on demand.
Technological Advancements Shaping the Market
Innovative technologies are set to enhance blow molding processes:
- Robotics and Automation: Automation will reduce labor costs and improve the precision and consistency of the production process.
- Advanced Materials: The development of stronger, lighter materials will enable manufacturers to produce more efficient container designs.
- Data Analytics: Integrating advanced data analytics will help manufacturers optimize production schedules and improve machine operational efficiencies.
Environmental Considerations and Sustainable Practices
As environmental concerns grow, the blow molding industry must adapt through sustainable practices:
- Recycling and Reusability: Manufacturers are looking to design products with recyclability in mind, reducing plastic waste.
- Energy-Efficient Machines: The shift towards machines that utilize less energy and reduce emissions will become a focal point for manufacturers.
- Material Innovations: The introduction of biodegradable materials will change how products are designed and perceived in the market.